Durable Concrete Flooring
Concrete can be ground, polished, and treated with engineered sealers and densifiers to create polished concrete. This is a modern flooring system that uses the treated and hardened concrete as the wear surface, so it is durable, renewable, and elegant. It is possible to touch up damage in the concrete and renew the surface if it ever gets worn. Stains and dyes can be applied to create colour and visual interest in the concrete floor. Polished concrete done correctly and maintained well can be the last floor your concrete surface will need.
Polished Concrete Types
There are a few general categories of polished concrete finishes:
- Exposed Aggregate Polish. This can be done in varying degrees, from full exposure to a light “salt & Pepper” finish. This showcases the colour and variation of the rocks used in the concrete, and can be used to hide imperfections in the floor by grinding them away. Cost for this can be higher because there is more tool wear and time involved in removing the concrete to get sufficient aggregate exposure. Polishes usually range from 800-3000 grit depending on desired gloss.
- Honed concrete. This is usually suited to exterior concrete, where a full polish may not be appropriate. It is similar to the exposed aggregate finish, except that the final grit is only taken to around 100 grit or so. Lower grit can allow for less visible wear and better traction in exterior use cases. Honing concrete is a great option to restore exterior concrete that has suffered minor spalling or other minimal surface damage, but is otherwise sound. Densification and sealing helps limit further damage, and the damaged concrete can be turned from an eyesore to a feature.
- Cream Polish. Only the top layer of the concrete is lightly polished, then sealed and densified. This can give a uniquely subtle colour and visual variation if the finishing and grinding are done correctly. This is best suited to floors that don’t require a lot of repair or patching, but is still possible with patching. Polishes are similar to exposed finishes above at a typical 800-3000 grit.
Densification and Sealing
All types of concrete grinding perform better with appropriate densification and sealing. Food safe surfaces are possible with the correct selection of densification and sealing treatments. Polished concrete is generally treated with a tandem densification and sealer system for strength and protection. The densification uses waterborne alkaline-earth silicates (Lithium, Potassium, & Sodium are common) to harden the existing concrete via a reaction with the existing free lime in the cement matrix to produce more C-S-H, which is one of the main constituents of cured cement. This has the effect of filling some of the pores and increasing the compressive strength of the top layer of concrete so it is more resistant to wear. Concrete pores are further filled by application of a penetrating sealer. Typically this is a silane based system, which is low maintenance, high performing and quite durable, but a little bit harder to work with than some of the other options, such as acrylic based or hybrid systems. Topical sealers should be avoided on polished floor installations as they may require more maintenance and generally won’t bond well.
Polishing new concrete
Considering a polished concrete installation from new allows a few options unavailable on polishing pre-existing slabs. Aggregate can selected for visual appeal, patterns of different stones or other objects can be embedded in the fresh concrete for exposure in the polishing process, and the concrete can be coloured integrally and/or with colour hardeners, which provide colour options unavailable in existing concrete. The finish troweling process can be varied with the final finish in mind if a cream polish is planned, for a visually appealing result.
A good result in a new polished concrete installation relies on doing the concrete well. This includes correct groundwork so the slab shifts minimally, appropriate rebar and sawcuts to control cracking, and correct mix design with minimal water and correct additives to control shrinkage and achieve optimal strength. Concrete should be appropriately cured prior to floor polishing and treatment for best results.
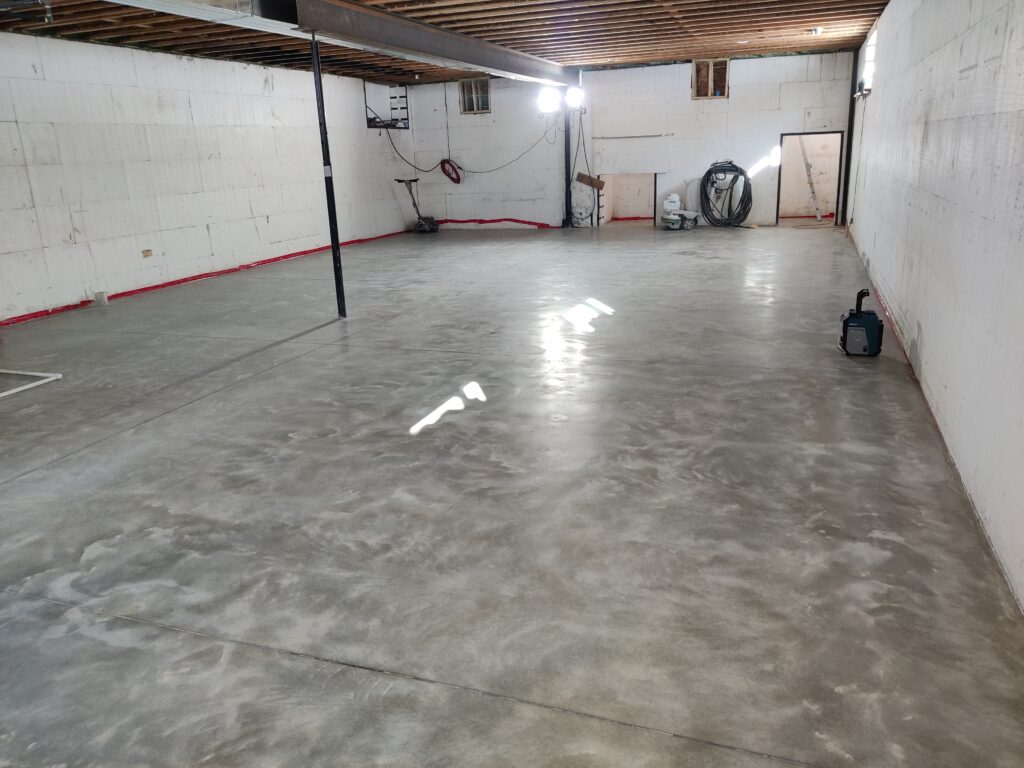
Polishing existing concrete
An existing concrete slab can still be a good candidate for concrete polishing. Heavier aggregate exposure can be used in conjunction with appropriate patching to renew and fortify existing concrete slabs. This is seen in some repurposed or renewed commercial and industrial spaces, where the durability and longevity of the polished floor makes it an economical system. A light polish and densification is sometimes used to protect new or lightly used concrete in heavy use cases. Basement developments and garage floors are also excellent candidates for a polished concrete floor. There are a lot of options for colour and finish to suit the final design.
Decorative and Colour Options
Here are a few of the decorative polished concrete finish options available:
- Concrete engraving can be used in tandem with different colouring methods to provide unique patterns.
- Acid stain or penetrating dye to colour concrete. Acid staining provides a colour variation unique to the slab based on the reactivity of the concrete substrate, while dye is more uniform.
- Integral colour and colour hardeners. These are only applicable during the initial pouring process, so are available only if the floor is planned from new as a concrete polish.
- Raw finish. This is an economical option that lets the existing floor materials shine through. It can be used elegantly in a cream polish.
- Aggregate variation & placement. This is only available on new concrete. Stone and sand can be varied to great effect, and unique patterns can be set into fresh concrete for exposure later. These can be applied to precast furniture or architectural concrete pieces such as countertops and hearths as well as floor slabs.
Decorative concrete is as unique as the slab it is performed on, and a polished concrete finish is no exception. Like a piece of leather, the variations and imperfections in the natural material will be visible, and add to the unique beauty of the piece. There are a lot of finish options available for a concrete polish installation if the selected craftsman has the knowledge and creativity to design and execute them.
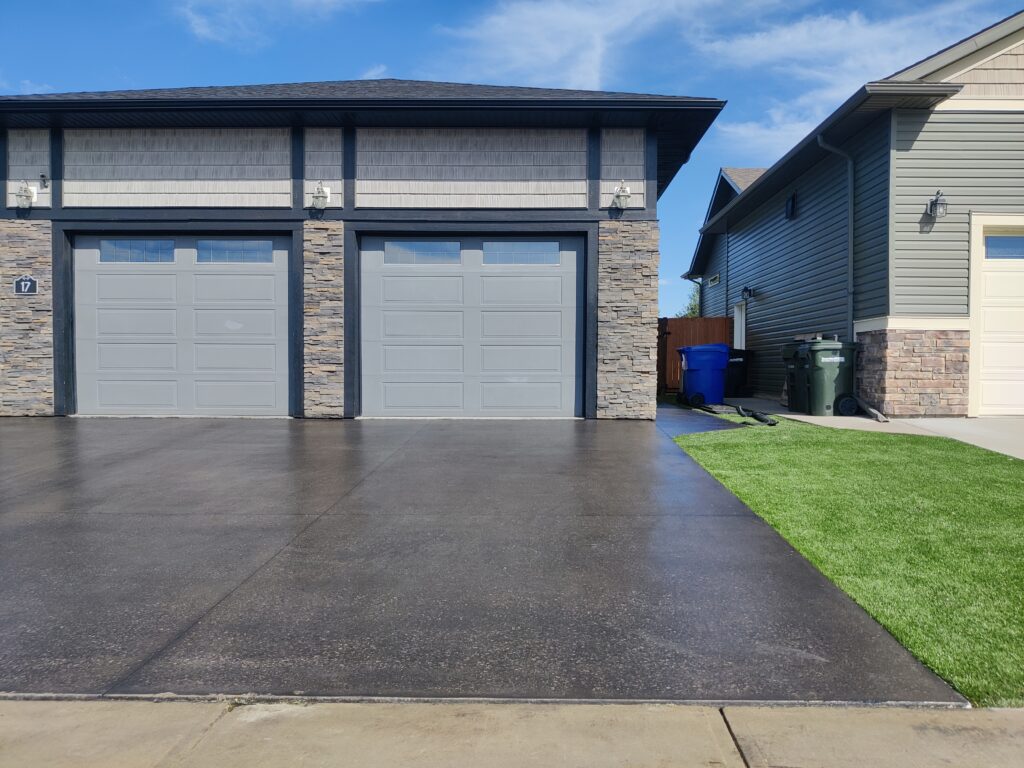
Polished Concrete Cost Comparison
Every polished concrete floor installation is a little different and will have it’s own pricing, but we can still make a few relative comments about the costs compared to other options. It is important to consider the useable lifespan and maintainability of a polished concrete floor when comparing it with other options. Polished concrete is repairable, renewable, and is one of the hardest wearing options available, so will outlast many other flooring options. This puts its long term running cost much lower than other systems.
In general, polished concrete will range around a medium to high end floor for cost to install. Initial cost will be a bit more than a good laminate floor, or comparable to a well done epoxy floor system for options such as cream polishes, which are great starting options for garage and basement floors. Higher end options such as full aggregate exposure with different colour treatments can be in the same class as a decent tile or hardwood floor installation. Costing varies with the condition of the concrete and final finish desired.
Contact us to learn more. We can help explain suitable concrete polishing options for your space, but will also let you know if other options might be more feasible.